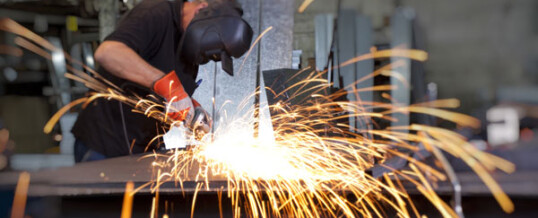
Nationwide, an estimated 600,000 manufacturing jobs are going unfilled, according to a survey published last year by Deloitte and The Manufacturing Institute.
The survey found 5 percent of current manufacturing jobs are unfilled due to lack of qualified candidates, 67 percent of manufacturers have a moderate to severe shortage of qualified workers, and 56 percent expect the shortage to increase in the next three to five years as older workers retire.
Most of these unfilled jobs are in the skilled production category — positions such as machinists, operators, craft workers, logistics managers and technicians.
How did the U.S. manufacturing industry – historically and currently the worldwide leader in manufacturing — lose its mojo? (Yes, the United States is the largest manufacturing country in the world and until recently the largest exporter). There are 14 million unemployed U.S. workers while there are more than a half –million job vacancies.
How did we get into this situation?
It comes down to two largely preventable trends.
The first is that the U.S. manufacturing industry has done a lousy PR job to attract today’s work force. Most people still envision workers bathed in sweat manually hauling raw materials to create appliances, cars, steel and other durable goods. But that no longer represents today’s manufacturing.
Advanced Manufacturing is the buzzword today. The Department of Labor’s Employment and Training Administration’s definition is as follows: “Advanced Manufacturing is the accelerated use of high-tech processes in the manufacturing plant.”
That means manufacturing workers today are relying on computerization, robotics and emerging technologies. This requires brain power, not brawn. This is the stuff that workers in the 20th century could never even imagine.
This is a story about innovation and creativity that isn’t being told to today’s younger workforce. It’s time that U.S. manufacturers sponsor road shows across the country to excite young people about manufacturing. They have a good story to tell: great jobs, great compensation and benefits, and great opportunities. And this must begin today if we are to catch up to the needs we face in filling high tech manufacturing jobs.
This takes us to the second preventable trend: taking the onus off of trade and technical schools. At one time, the U.S. had apprentice programs where workers trained to become craftsmen and skilled artisans. Yesterday’s apprentice programs are today’s trade and technical schools.
Unlike traditional colleges, where students must complete a wide variety of courses, many of which are unrelated to their desired jobs, a trade school offers a highly focused curriculum devoted exclusively to preparing a student for their job of choice. A trade school student will generally earn their degree in a shorter amount of time than in a traditional college and at a much lower cost.
Yet, even as enrollment in trade schools is increasing, the Obama administration seeks to reduce funding for vocational training by 20 percent, while concentrating primarily on the Pell Grant program that offers financial aid for college and university attendance. If you look at the millions of college graduates that are unemployed or under employed, why wouldn’t the government want to put more emphasis on trade school students, who tend to be from lower income backgrounds and thus more dependent, directly or indirectly, on government assistance?
According to data, England, Germany, Japan and Sweden invest as heavily in the education and training of work-bound youth as they do for each college-bound youth. This puts the U.S. at a disadvantage when it comes to filling and creating today’s manufacturing jobs.
When 600,000 jobs are unfilled and 14 million unemployed, this nation must re-evaluate its commitment to manufacturing. It has been the backbone of this country from its very founding and to allow the U.S. to slip behind other countries in manufacturing superiority is unconscionable.
The United States must re-claim its manufacturing leadership. We have the smarts, we have the workers, and we have the resources. What we lack is the will.
MAR